Mind the gap: extending ERP through MES integration
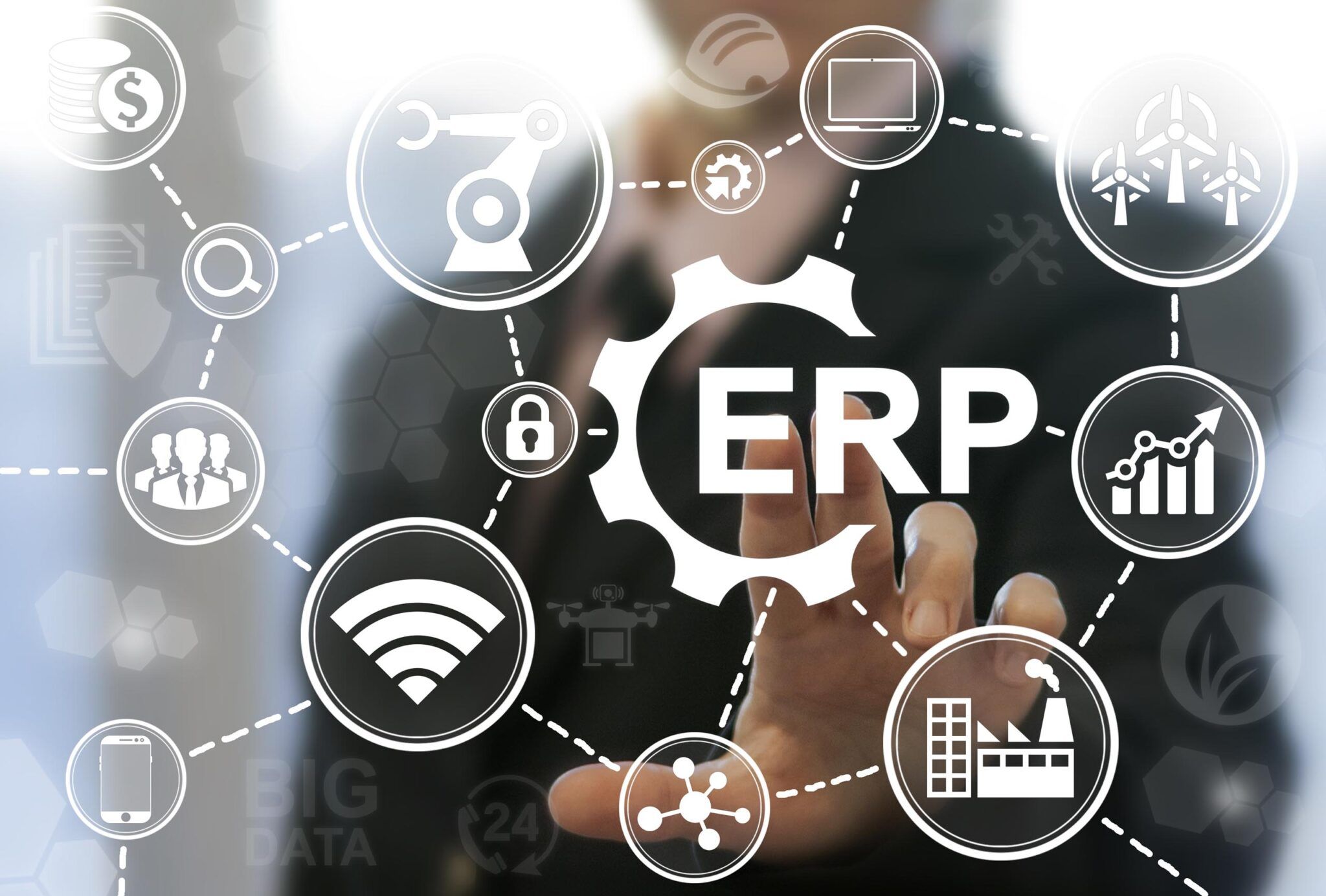
Tools that from a high-level perspective perform many similar functions, which is why they can often be referred to in an ‘either/or’ context.
The reality, however, is that these solutions are designed with very distinct purposes in mind. Overlaps do occur, but the outcomes certainly don’t, as both are designed to fulfil separate aspects of the overall manufacturing process.
That’s why the argument should be less concerned with either/or, and more focused on how one helps extend the other to offer complete end-to-end coverage into performance – from the shop floor to the finance team and beyond.
Different by design
Let’s start with some basic definitions to help establish ‘boundaries’ of responsibility:
- ERP (Enterprise Resource Planning) is technology – typically driven by finance or IT departments – that’s used to manage operations such as plant scheduling, order processing, and inventory management. It’s essentially a system of record that provides a detailed window into operational conditions and business performance
- MES (Manufacturing Execution System) provides a more granular level of detail into conditions on the shop floor, including data on all factors impacting the assembly line – with the resulting insights used to drive performance, compliance, workforce, and machine productivity
Similarities between the two solutions can of course be found. But it’s the differences that really matter. Chief among these is that ERP in the main looks at events after they’ve happened, whereas a MES system is delivering a real-time view – which is why they can work so well together.
Closing the gap
ERP systems are primarily designed to aggregate data in support of high-level finance decisions. This detailing of the ‘what’ is of course an important function, but it often leaves manufacturers short of insight into the ‘when’, ‘how’, and (most importantly) the ‘why’.
What’s more, with only limited coverage of real-time shop floor processes, an ERP-only environment will create a blindspot in terms of what’s actually happening day-to-day. Without an MES in play, the process of adapting schedules and collecting real-time information from both the operatives and machines etc. will inevitably be conducted via disconnected spreadsheets or (more commonly) paper-based records.
That’s not to suggest however that ERP systems cannot be adapted to counter this digital shortfall. But doing so demands huge levels of customisation, which comes with eye-watering cost implications – alongside the demand placed on IT to manage this highly bespoke arrangement. The final result is a system that’s not designed to offer the ease-of-use operatives demand, a fact that often leads to poor uptake and user adoption.
From reactive to proactive
That’s enough of the problem. Let’s turn our attention instead to the solution. The good news here begins with the fact that a modern MES solution will neatly integrate with all standard ERP technologies. MESTEC for example uses flat file or API integration capabilities to both push and pull data from the ERP layer. Once this happens, the linear world of ERP enters more responsive, visual, drag and drop, representation of exactly what happens on the production floor.
As for the nature of the ‘dual partnership’ formed by a MES and ERP system, the value can be highlighted in four key areas:
- Scope and Functionality: focused on the manufacturing process, a MES will manage shop floor activities such as production scheduling, job tracking, quality control, and inventory management. ERP extends this insight by covering a broader range of functions such as finance, HR, procurement, and supply chain management.
- Data Focus: MES focuses on providing real-time information on the shop floor, collecting data on the status of each job, the progress of production, and the performance of machines and operators. ERP systems, typically unable to handle real-time data, are more geared toward data that is batch processed and delivered at set intervals.
- Integration: MES integrates with systems such as PLCs (Programmable Logic Controllers), SCADA (Supervisory Control and Data Acquisition), and LIMS (Laboratory Information Management Systems) to provide a complete solution for managing operations. Whereas ERP collects the aggregated information from various systems to provide an overall snapshot view of the business.
- Decision-making: the real-time data delivered by MES enables managers to track production progress, identify bottlenecks, and adjust operations accordingly. In support of this, ERP turns the focus toward quantitative financial analysis.
As the above highlights, ERP and MES software have one enormous difference: time scale. While ERP works in hours, days, weeks, MES works in minutes or even seconds – with ERP concerned with daily or weekly production and MES on the real-time operational reality.
Complementary capabilities
MES can therefore extend ERP in a number of highly significant ways. Operators and managers have access to real-time scheduling and shop floor insights, and through them a wealth of performance KPIs such as actual versus standard, labour efficiency, work in progress, on-time delivery, and overall equipment effectiveness.
This combination of a powerful ERP system and MESTEC’s dynamic MES system, can therefore provide a total solution for optimising performance and driving operational productivity. That’s a win-win in anybody’s book.
To find out more about MESTEC’s ability to extend your ERP investments, come and see us on stand D68.